-
Daniel WereeHave been business relationship for 3 years, great partner for Nickel Cobalt Alloy!
-
Carolina FasioOn-time delivery. And support is good and fast.
K94840 Iron-Nickel Soft Magnetic Alloy Highest SaturationFlux Density FeNi Alloy
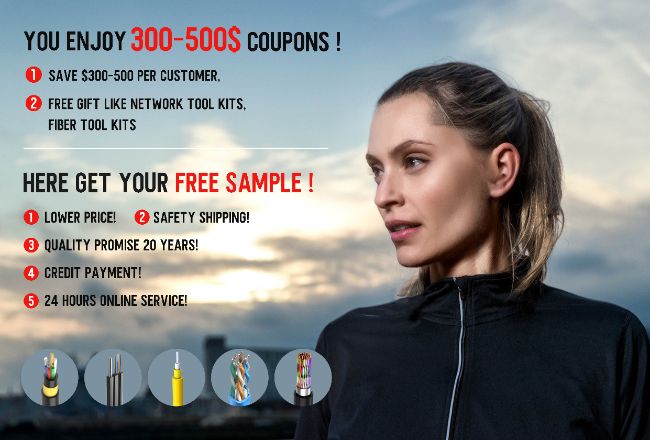
Contact me for free samples and coupons.
WhatsApp:0086 18588475571
Wechat: 0086 18588475571
Skype: sales10@aixton.com
If you have any concern, we provide 24-hour online help.
xEqual Grade | 1.3922, K94840 | Trade Name | HIGH PERMEABILITY 49, IMPHY® SUPRA 50, FeNi48 |
---|---|---|---|
Spec | ASTM A753, ASTM F30 | ||
Highlight | Highest SaturationFlux Density FeNi Alloy,K94840 FeNi Alloy,K94840 Soft Magnetic Alloy |
K94840 is a 48% nickel-iron alloy that possesses the highest saturation flux density of any nickel-iron alloy. The saturation flux density of about 16000 gauss (1.6 Tesla) combined with high magnetic permeability and low core loss makes this a versatile alloy with many potential applications.
K94840 has been used in laminated cores for instrument transformers, magnetic shields and cores for certain electronic and communications devices in which extremely high permeability at low magnetizing forces greatly increases the efficiency and effectiveness of the equipment.
Because of its high permeability, it has also been used in solenoid cores and sensitive relays that must respond to low magnetizing forces
Chemical composition
Element | C | Mn | Si | P | S | Cr | Ni | Mo | Co | Cu | Fe |
Wt, % | 0.05 | 0.80 | 0.50 | 0.03 | 0.01 | 0.30 | 47-49 | 0.30 | 0.50 | 0.30 | rem |
Key Properties:
- High saturation flux density
- High magnetic permeability
- Low core loss
Applications
- Actuators
- Gas safety valves
- Ground fault circuit breaker (relay parts)
- High precision current transformer cores
- Safety valves
- Relays
- Resolvers
- Sensors
- Shielding
- Watches
- Instrument transformers
- Sensitive relay and solenoid components
Specs
- 1.3922
- 1.3926
- K94800
- K94840
- DIN17405
- ASTM F30
- ASTM A730
- IEC 404
- JIS C2531
- ASTM A753 Standard Specification for Wrought Nickel-Iron Soft Magnetic Alloys (UNS K94490,
- K94840, N14076, N14080)
- MIL-N-14411B (MR) (Composition 3 and 4)
Heat treatment
Standard hydrogen anneal
For maximum softness and optimum magnetic and electrical properties, K94840 should be annealed in an oxygen-free, dry hydrogen atmosphere with a dew point below -40°F (-40°C) for 2 to 4 hours at 2150°F (1177°C), followed by a furnace cool at a rate of 100/200°F (55/110°C) per hour down to 800°F (427°C) and at any rate thereafter.
Oil, grease, lacquer, and any other contaminants must be removed before annealing. During hydrogen annealing, the individual parts should be separated by a surface insulation media or an inert insulating powder, such as magnesium or aluminum oxide.