-
Daniel WereeHave been business relationship for 3 years, great partner for Nickel Cobalt Alloy!
-
Carolina FasioOn-time delivery. And support is good and fast.
UMCo-50 Nickel Based Alloys Shock Resistance Wear Resistance China Origin Fast Delivery
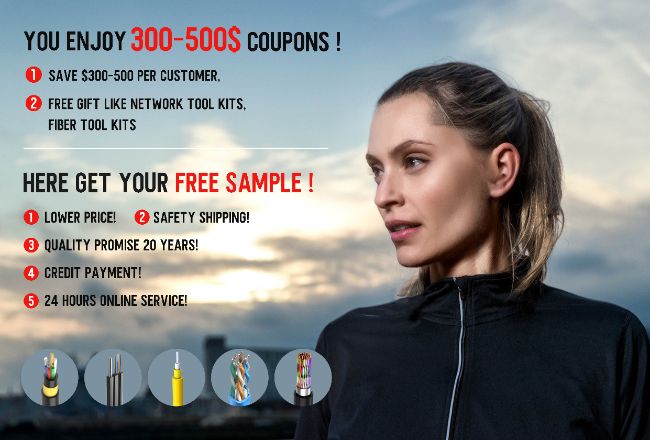
Contact me for free samples and coupons.
WhatsApp:0086 18588475571
Wechat: 0086 18588475571
Skype: sales10@aixton.com
If you have any concern, we provide 24-hour online help.
xEqual Grades | Thermco50, W.Nr. 2.4778, Co50, G-CoCr28 | Form Of Supply | Forging, Tube,rod,pipe |
---|---|---|---|
Grade | UMCo-50 | Chemical Composition | 50Co-30Cr-20Fe |
Product Name | Nickel Based Alloys | Certification | ISO9001:2015 |
Highlight | UMCo-50 Nickel Based Alloys,G-CoCr28 Nickel Cobalt Alloy,ISO9001 Nickel Based Alloys |
UMCo-50 With High Temperature Thermal Shock And Wear Resistance
UMCo-50 Co50 with High Temperature Thermal Shock and Wear Resistance
UMCo50 is a heat-resistant cobalt alloy with excellent thermal shock resistance and wear resistance performance. It has great strength against sulfur-and vanadium-attacks. UmCo-50 has higher melting point compared to other cobalt based or nickel based heat-resistant alloys.
For example, the alloy used for skid rails at a steel mill undergoes regular use at 1350°C,so other alloys could not be used due to their low melting point in the application related to heat treatments and furnaces. But UMCo-50 shows successful results.
UMCo-50 (Co50) is suitable for the environments that require oxidation resistance,high temperature strength and thermal corrosion resistance, thermal impact resistance and wear resistance.
In a sulfur-containing oxidation atmosphere, it has an excellent thermal corrosion resistance to heavy oil or other fuel combustion medium. It is widely used in coal chemical nozzle.
Chemical Composition (%, EN 10295)
C | Si | Mn | P | S | Cr | Mo | Ni | Nb | Co | Fe |
0.05-0.25 | 0.50-1.50 | 1.5 | 0.04 | 0.03 | 27-30 | 0.50 | 4.0 | 0.50 | 48-52 | 余 |
Equal grades
Thermco50, W.Nr. 2.4778, Co50, G-CoCr28
Main characteristics
High Temperature Resistance, Thermal Shock Resistance , Wear Resistance
Higher melting points than other cobalt based and nickel based alloys (1380 -1395 °C)
Corrosion resistant in Sparse sulfuric acid and boiling nitric acid and corrosion rapidly in hydrochloric acid
Shock Resistances
Since thermal shock resistance was given first priority when developing UMCo-50, this alloy shows far more outstanding thermal shock resistance than the popularly used 25Cr-20Ni stainless steel. For example, even after repeating the heating and cooling cycle (1000-water cooling-7 seconds) for 500 times, no cracking occurred. As a practical example, the alloy was used for four and a half years as a tray which was heated up to 1000 in a heavy oil furnace to quench various quenching agents. Hardly any cracking occurred in UMCo-50, whereas the 25Cr-12Ni alloys were able to be used for only 8 months in average.
Wear Resistances
As for the wear resistance of UMCo-50, hardly any deterioration was found after being used as a sintering bar for copper sulfide for 50 months. On the other hand, cast iron parts used till then were heavily corroded, oxidized and worn even though operations were conducted at 900, making them usable for only three and a half months.
Form of supply
Rods, forgings, seamless pipes, tube, etc
About XUNSHI
Suzhou Xunshi New Material Co. Ltd- referred as XUNSHI hereafter, is a professional manufacturer of high-performance alloy products. XUNSHI is engaged in supplying high quality and cost-effective Superalloy, Anti-Corrosion Alloy, Precision Alloy, Special Stainless Steel and Magnetostrictive Material to customers worldwide.
Why XUNSHI
· Highly experienced in alloy industry
· Top experts of industry in China
· Advanced technology and process from top famous institutes in China
· Advanced devices through whole production and inspection process
· Strict quality control system
· Company motto: best service, most value
· Smart sales policy
Service Items of XUNSHI
· Non-standard product research and pre-production
· Fabrication of products
· Cutting, splitting for sheets and plates in stock
· Heat treatment (Solution treatment, aging harden treatment, anneal, spring temper, quench etc.)
· Surface finish (peeling, gridding, polishing)
· Logistics service
· Customized packing service (also for exporting)
· Import and export (XUNSHI is certificated)
· Document translation
· Hard-to-find material sourcing
Customers of XUNSHI
Customers of XUNSHI are all over China (Taiwan and Hong Kong included). And we are exporting to USA, Canada, Italy, UK, Poland, Greece, Russia, Turkey, Iran, Israel, South Africa, South Korea, North Korea, India, Argentina, and Brazil and so on. Customers from 30+ countries trust us.
Where is XUNSHI
A- XUNSHI is in Huaqiao, Kunshan, 215332 China, which is very closed to Shanghai.
B- Xunshi is around 80KM from Shanghai Pudong International Airport (PVG).
C- 20KM from Shanghai Hongqiao Airport
D- 20KM from Shanghai Hongqiao Railway Station
E- You can contact XUNSHI sales for a pickup service.