-
Daniel WereeHave been business relationship for 3 years, great partner for Nickel Cobalt Alloy!
-
Carolina FasioOn-time delivery. And support is good and fast.
Nimonic 75 Alloy Heat Corrosion Resistance For Gas Turbine Engineering
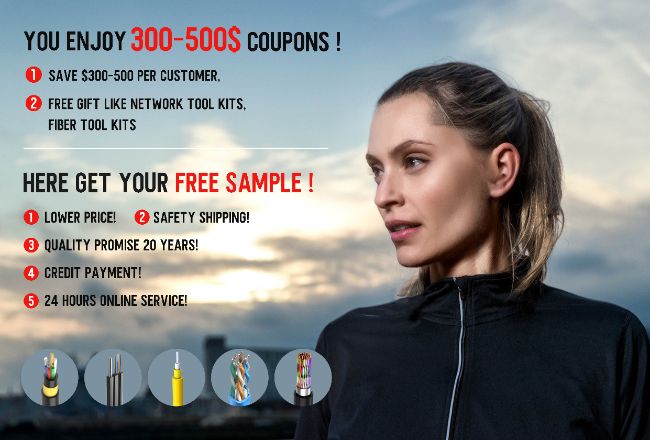
Contact me for free samples and coupons.
WhatsApp:0086 18588475571
Wechat: 0086 18588475571
Skype: sales10@aixton.com
If you have any concern, we provide 24-hour online help.
xEqual Grade | UNS N06075, W.Nr. 2.4951 & 2.4630 | Forms Of Supply | Bar, Forging, Wire, Plate, Pipe |
---|---|---|---|
Density | 8.37g/cm3 | Melting Range | 1340-1380°C |
Electrical Resistivity | 1.09 µΩ•m At 20°C | Product Name | Nimonic 75 Alloy |
Highlight | nickel chromium alloy,nimonic 90 bar |
Nimonic 75 Nickel-Chromium Alloy with Good Corrosion and Heat Resistance
NIMONIC 75 is an 80/20 nickel-chromium alloy with controlled additions of titanium and carbon. First
introduced in the 1940s for turbine blades in the prototype Whittle jet engines, it is now mostly used for
sheet applications calling for oxidation and scaling resistance coupled with medium strength at high
operating temperatures. It is still used in gas turbine engineering and also for industrial thermal processing,
furnace components and heat-treatment equipment. It is readily fabricated and welded.
Chemical composition
Element | C | Cr | Cu | Fe | Mn | Si | Ti | Ni |
Weight(%) | 0.08~0.15 | 18.0~21.0 | 0.5 max | 5.0 max | 1.0 max | 1.0 max | 0.2~0.6 | Rem |
Advantages
- Good corrosion resistance
- Good heat resistance
- High temperature static applications
Applications
- Sheet applications calling for oxidation and scaling resistance coupled with medium strength at high operating temperatures
- Gas turbine engineering
- Industrial thermal processing, furnace components and heat-treatment equipment
Heat-Treatment
For bar 30-60 minutes at 1050°C (1920°F) followed by air cooling.
For sheet 5-10 minutes at 1050°C (1920°F) followed by air cooling or, before welding, 5-10 min/1050°C
(1920°F)/AC + an optional 10 min/1050°C (1920°F)/AC.
Forms of supply
Bar, wire, rod, forging, plate, strip, sheet, pipe
About XUNSHI
Suzhou Xunshi New Material Co. Ltd- referred as XUNSHI hereafter, is a professional manufacturer of high-performance alloy products. XUNSHI is engaged in supplying high quality and cost-effective Superalloy, Anti-Corrosion Alloy, Precision Alloy, Special Stainless Steel and Magnetostrictive Material to customers worldwide.
Why XUNSHI
· Highly experienced in alloy industry
· Top experts of industry in China
· Advanced technology and process from top famous institutes in China
· Advanced devices through whole production and inspection process
· Strict quality control system
· Company motto: best service, most value
· Smart sales policy
Service Items of XUNSHI
· Non-standard product research and pre-production
· Fabrication of products
· Cutting, splitting for sheets and plates in stock
· Heat treatment (Solution treatment, aging harden treatment, anneal, spring temper, quench etc.)
· Surface finish (peeling, gridding, polishing)
· Logistics service
· Customized packing service (also for exporting)
· Import and export (XUNSHI is certificated)
· Document translation
· Hard-to-find material sourcing
Customers of XUNSHI
Customers of XUNSHI are all over China (Taiwan and Hong Kong included). And we are exporting to USA, Canada, Italy, UK, Poland, Greece, Russia, Turkey, Iran, Israel, South Africa, South Korea, North Korea, India, Argentina, and Brazil and so on. Customers from 30+ countries trust us.
Where is XUNSHI
A- XUNSHI is in Huaqiao, Kunshan, 215332 China, which is very closed to Shanghai.
B- Xunshi is around 80KM from Shanghai Pudong International Airport (PVG).
C- 20KM from Shanghai Hongqiao Airport
D- 20KM from Shanghai Hongqiao Railway Station
E- You can contact XUNSHI sales for a pickup service.